1, vertical flow: In the vertical surface coating, the coating flow is downward, convex phenomenon, poor coating effect. Causes: It may be too thick or too thick at one time, too high paint concentration, too much air in the spray gun, too much paint, and the nozzle is too close to the coating. Countermeasures: Diluted excessive viscosity, adjusted spray gun gas, pressure 3.5-4.5kg/m2, pressure appropriate and output, distance appropriate (15cm-20cm). 2, brush marks: After brushing, the film is stripped uneven phenomenon. Cause: During construction, the viscosity is too high and the wet film is recoated. Solution: Adjust the paint to an appropriate viscosity. When coating, the base film must be substantially dry, and the brush should not be excessively strong. 3. Pinhole: After the coating is dried, the coated surface shows a small hole, and the pinhole is formed by the surface of the substrate. Causes: The coating film is sprayed too thick, the drying temperature is too high, the coated object has moisture, dust paint, etc. Countermeasures: Spray thickness should not be too thick at one time, control the proper drying temperature, and keep the object to be coated without dirt. 4. Dry spray phenomenon: When the paint is sprayed, the atomized paint will not dry until it is coated, and it will form a rough surface when it is attached. Cause: The distance between the spray gun nozzle and the object being painted is too long, and the air pressure of the gun is too high. Countermeasures: Adjust the distance between the spray gun mouth and the object to be coated, about 15cm-20cm, and the pressure is adjusted to 3.5-4.5kg/m2. 5. Whitening phenomenon: The surface of the coating film is pale and there is no expected luster. Cause: The humidity is too high (80% or more), the thinner is too fast, and the object is too cold. Countermeasures: Painting humidity should be more than 80%, or can add 5-10% of anti-white water, to use fast-drying thinner, not too cold coated objects. 6. Peeling off: The coating film falls from the surface of the object to be coated. Causes: The substrate contains wax, oil, water, etc. The undercoating is not dry and it is painted again. The substrate is too smooth and the wall surface has been powdered or used with poor soil and adhesion. Countermeasures: Thoroughly remove the substrate and ensure that there are no waxes, oils, water, and other debris. The old wall that has been pulverized must be removed. The oily batch of soil, or the water-based batch of soil, should be flat and completely dried and then coated. 7, orange peel phenomenon: The coating is not smooth, like orange peel bump coating. Causes: The diluent evaporates too quickly, the spray pressure is variable or the pressure is too high, the blowing distance is too far, one spray is too thick, and the bottom layer is not dry before painting. Solution: Use appropriate diluent to control the gun pressure. The distance should be moderate. Do not apply a thick coating. The bottom layer is completely dry and then painted. 8, fade phenomenon: After a few days of coating, the color part fades, the color is not uniform. Cause: The new addition is not completely dry, and the alkali is too heavy, causing the color to fade. Countermeasures: The new wall should be painted one month later with an epoxy primer.
Three trees lacquer paint
High quanlity Aluminum die casting Auto/Motors parts
Automatic lathes and presses for our production.All surfaces are finished just as you have specified.
Our tool workshop, extrusion workshop, machined workshop, anodized workshop, packing workshop and sales will provide you all solutions of your products.
Using Machine:Die casting machine 120 ton -800 ton
Main Processes Flow(depends on part shape and requirement):
Drawing / or Samples →Mould making →Die casting →Deburring →Drilling and Tapping →CNC Machining →Polish →Surface treatment →Assembly →Quality inspection → Packing →Shipping
Production Flow:
Drawing/ or samples → Mould making →Die casting and other processes →Get samples and send samples to customer for confirm → Mass Production ( casual inspection avoid unintentional situation) → QC → Packing →Shipping →Cycle to next order
Surface Treatment (Optional by customer):
Polishing, Sandblasting, Painting, Powder coating, Galvanizing, Chrome plating
Anodizing , Real gold coating, Imitation gold.

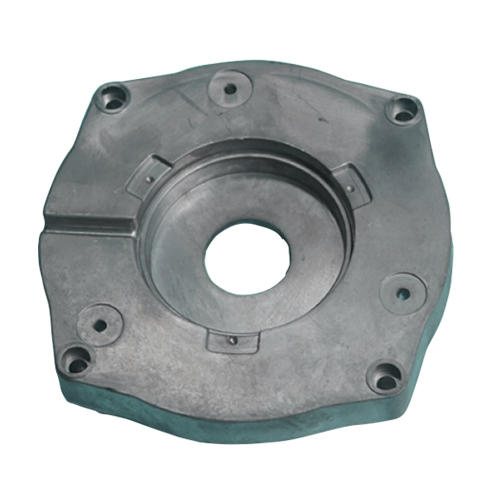
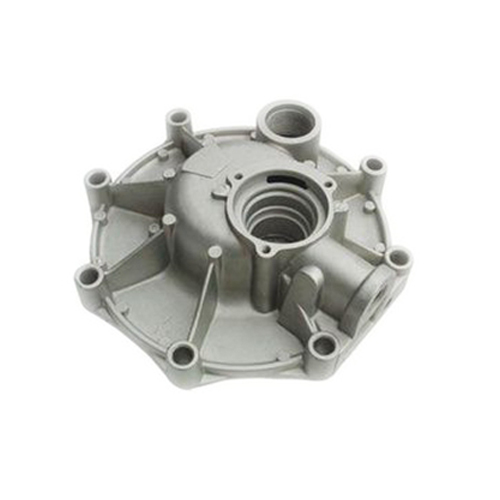
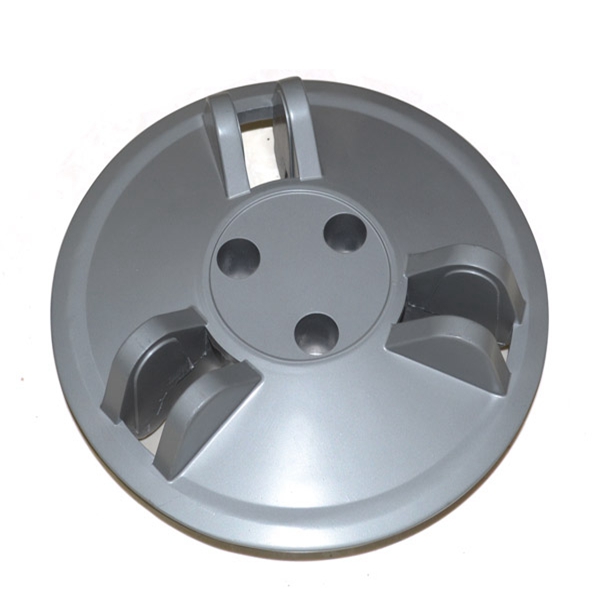
Aluminum Auto/Motors parts
Motor Box,Casting Motorcycle Parts,Alloy Motors,Motor Casting
Dongguan Hongge Hardware Technology Co., Ltd , http://www.honggecasting.com