According to the latest research by the German Federation of Machinery and Equipment Manufacturing (VDMA), China's mechanical engineering market will undergo a rapid change in the next few years, especially the mid-end market will develop rapidly. According to VDMA data, the proportion of the mid-end market in the entire market will increase from 34% to 40% in the next three to five years. In this regard, machine tool manufacturer EMAG provides Chinese customers with a range of solutions to adapt to market development. The spindle automatic loading and unloading technology is the basis of the machining concept tailored by EMAG to the Chinese market. Its simple automation concept guarantees flexible, stable and high-volume production of parts. Its emergence will enable those who use artificial Loading and unloading and complex processing system equipment retreated to the second line of production.
Spindle automatic loading and unloading core advantages
As early as the 1990s, EMAG began to develop the innovative technology of automatic spindle loading and unloading. Over the years, EMAG has opened up many new applications in this area of ​​technology and has continuously improved its processes. The basic principle of the automatic spindle loading and unloading system is to transfer the workpiece to the machining area through the working spindle to realize the integration automation, followed by high-speed different processing. The entire process is extremely short and requires only one setup. What is the core of this technology's success? Mr. Christoph Hoene, Director of EMAG Asia Pacific, responded with the words “simplicity and flexibilityâ€: “Although the automation technology we use may be simpler, we have the flexibility to do a lot of operations.â€
Automated solutions, comparisons can be better understood
Taking the three elements of OEE (equipment comprehensive efficiency), namely the effective utilization rate of the machine tool, the production efficiency and the quality of the parts it manufactures, the principle of automatic spindle loading and unloading is compared with other competitive technologies, which can be seen more directly. Technical advantage. In the case of multi-layer manufacturing systems, they often use robots or complex clamping systems to connect individual machine tools. However, it is very common that the workpieces in such systems are very difficult to manipulate, so operations are extremely disruptive; frequent interruptions can greatly reduce system utilization. The use of spindle automatic loading and unloading technology can save some of the commonly used automation systems, and can ensure the stability and accuracy of the entire production process. The transfer of the workpiece between the machine tools is done via a conveyor belt or reciprocating conveyor system behind the machining area. A simple automation module picks up the workpiece from the conveyor and places it in the diamond frame of each machine. The rest is done by the spindle. Compared to other solutions, the amount of automation can be increased by 15% to 30%, while the custom machine design ensures the safety of the production process, thus ensuring high machine utilization. In terms of productivity, the stroke between these compact loading and unloading devices is very short, ensuring that the delivery time of the components is kept to a minimum, thus ensuring the highest yield in a given time. Mr. Hoene said that by examining other relevant technologies on the market, EMAG's specialized manufacturing systems with spindle loading and unloading equipment have a high yield advantage compared to the output of complex connection technology solutions.
Pure manual loading, or partial automation?
Whether it is a multi-layered production line or a stand-alone application for a single machine, EMAG automation technology enables a high degree of flexibility in its production. In the case of manual loading, the operator can manually insert the clamped part into the diamond frame, and then the diamond frame is sent to the loading and unloading station, and the operator removes the finished part from the diamond frame.
What makes manufacturers rely on this partially automated process? Is it easier to use a horizontal lathe for manual loading? Mr. Hoene explained: “This is especially evident when we look at the OEE element of component quality. There are many risks associated with pure manual loading, which can lead to clamping errors. For example, in the automotive field, 1μm nuances will The quality of the components is determined. In the production process of horizontal machine tools, the advantages and disadvantages of the components depend largely on the capabilities of the operators. With this in mind, the automatic spindle loading and unloading solution is the best choice. Because it can make the clamping and machining of the workpiece extremely accurate, it can even be equipped with a measuring system for quality supervision as needed, so as to minimize the possibility of error (see Figure 1).
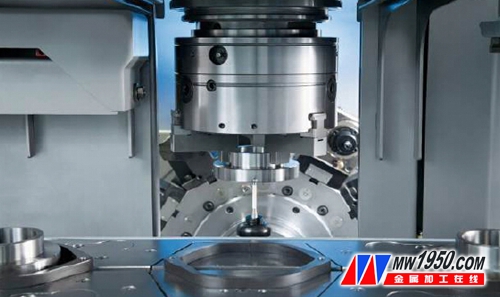
Figure 1 Optional measurement tool
Figure 1 shows the optional measuring tool. The measuring probe located outside the machining area performs on-line quality control. Before the machining is completed and returned to the belt, the machine automatically measures the workpiece and plays the role of online quality control.
Integration responds to future challenges
Technological development has also played a very important role in influencing the efficiency of machine tools. In the automotive industry, for example, many transmissions and engine components have undergone tremendous changes, more and more miniaturized, and the shape and structure have become more complicated. Nonetheless, all relevant production processes must maintain high productivity at the same time. “If the new machine tool declines in productivity after a few years and no longer meets the ever-changing production needs, it will have a negative impact on the overall efficiency of the equipment,†Mr. Hoene stressed. The flexibility of the machine tool is very important for EMAG developers. They use a modular design to configure each machine so that it can be adapted to a specific task, and each process and its automation can be transformed as needed. This ensures that the system can be adjusted at any time to cope with the increasing volume or production of different workpiece sizes. Figure 2 shows the new production system developed by EMAG – the gear production system, which has left a deep impression on customers in terms of convenient wiring, working speed and design flexibility, turning, hobbing and deburring – The modular design precisely configures each machine for assigned operational tasks.
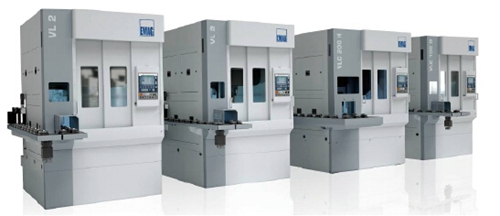
Figure 2 EMAG gear production system
In the face of rapid technological changes in many fields, EMAG considers this to be a very good market opportunity. Mr. Hoene said: “We have the ability to customize parts loading and unloading solutions according to customer needs. The efficiency of this system is not comparable to other automation technologies. This is a decision to win or lose.â€
Infrared transponder:Support wifi, 433 communication frequency, support phone remote control, intermediate point limit function, built-in control module, control ability, strong anti-jamming capability, ultra-quiet operation, suitable for high quality electric screen, family office and other places of business
Wireless socket:
Applicable to wifi, Zigbee protocol, using 16 a large current design, support mobile phone remote control and manual control, compatible with all kinds of electric equipment, can be real-time detecting the power capacity of the home appliances and electric current, statistical power, simple configuration, used in family, office space and so on need to remote control of electrical appliances
Include following devices:
1.wifi wall socket
2.ZigBee wireless socket
Smart Home Wall Socket
Smart Home Wall Socket,Socket Smart Switch,Smart Electric Wall Socket,Intelligent Wall Socket
Shenzhen Zhuohao Intelligent Electronic Development Co., Ltd. , https://www.szactop-smart.com