h Dmin = r(1-cosq) | (1) |
As can be seen from Figure 2, q+w+b=90°, ie
q =90°-(w+b) | (2) |
W——the angle between the direction of the normal stress and the direction of the cutting speed. The value of w is related to the strength, elongation, friction coefficient and the position of the point A of the workpiece material. According to the experience, w=38°~45°.
Substituting equation (2) into equation (1) is simplified:
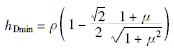
h Dmin | w =38° | w =40° | w =42° | w =45° |
---|---|---|---|---|
μ=0.12 | 0.295r | 0.271r | 0.246r | 0.214r |
μ=0.26 | 0.206r | 0.158r | 0.165r | 0.138r |
According to experience, w=42° can be taken, and when μ=0.12~0.26, h Dmin =(0.165~0.246)r.
It can be seen that in order to achieve ultra-thin cutting with a cutting thickness of nanometer, the radius of the cutting edge of the diamond tool used at this time should be 4-6 nm, which is a tool with a very small cutting edge and extremely sharp.Cutting temperature effect
Due to the extremely small amount of cutting for fine cutting and the high thermal conductivity of diamond tools and workpiece materials, the cutting temperature for fine cutting is quite low compared to conventional cutting. However, for ultra-fine machining with extremely high precision, the influence of small changes in machining temperature on machining accuracy is not negligible. At the same time, the cutting temperature has a great influence on the tool wear, and the cutting temperature has a significant influence on the chemical wear of the diamond tool.The complexity of the micro cutting process
Extremely small depth of cut (nanoscale), limited edge radius, low ratio of cutting thickness to cutting edge radius, cutting edge quality, and small tool wear on the flank face all complicate the ultra-fine machining process. Deformation of the three deformation zones, especially the tool-to-workpiece friction in the third deformation zone and the recovery of the tool surface due to the elastic recovery of the machined surface, resulting in cutting heat, affecting the integrity of the machined surface and causing subsurface damage . When the cutting thickness is on the same order of magnitude as the cutting edge radius, the effect of the sliding and ploughing phenomenon due to the change of the tool rake angle (negative rake angle) on the cutting process is also obvious.3 Technical difficulties in ultra-fine machining
Micro-machining mainly refers to the processing of fine-sized parts with a part size of 1 mm or less and a machining accuracy of 0.01 to 0.001 mm; ultra-fine machining refers to the processing of ultra-fine parts with a size of 1 μm or less; nano-scale ultra-fine processing is Refers to the processing of parts with a fineness of 1 nm or less. The realization of nano-scale ultra-fine machining mainly has the following technical difficulties:Effect of material micromachining
The material removal process depends not only on the cutting tool, but also on the material being processed itself. The choice of ultra-fine machining materials is based on the premise of nano-scale surface quality, which is called “micro-machining†of materials (defined by nano-scale surface roughness and negligible tool wear at a certain machining distance). Factors affecting the micro-processability of the material include the internal affinity (chemical reaction) of the material to be cut by the diamond tool, the crystal structure of the material itself, defects, distribution, and heat treatment state (such as the anisotropy of the polycrystalline material on the surface of the part) Integrity has a greater impact).Large unit cutting force
Micro-cutting is an extremely thin cutting, and the cutting thickness may be smaller than the size of the crystal grains. Therefore, the cutting force is characterized by a small cutting force, but the unit cutting force is very large. The physical essence of achieving nano-scale ultra-fine processing is to cut the bonds between molecules and atoms of the material to achieve the removal of atoms or molecules. Therefore, the cutting force must exceed the molecular and atomic bonding forces inside the crystal. When the cutting depth and the feed amount are extremely small, the cutting force per unit cutting area will increase sharply, and at the same time, a large amount of heat is generated, and the temperature of a local portion of the tip end of the blade is raised, so that the tool is required to be high during fine cutting. Ultra-hard tool materials with high wear resistance, heat resistance, high temperature hardness and high temperature strength are required. When cutting non-ferrous metals such as aluminum alloys, diamond tools are most commonly used.Limit of the radius of the cutting edge on the thickness of ultra-micro cutting
The tool edge radius limits its minimum cutting thickness, and the smaller the tool edge radius, the smaller the minimum allowable cutting thickness. As can be seen from Table 1.Tool wear and tear
Due to the micro-wear of the diamond tool, the tool wear will gradually increase after a certain period of cutting, and sometimes it will suddenly deteriorate. There are two forms of failure of diamond tools: chipping and wear. The mechanical wear and micro-cracking of diamond tools are caused by microscopic cleavage at the edge of the blade, and the nature of the wear is the accumulation of microscopic cleavage. Accumulated diamond tool wear occurs primarily on the front and back flank of the tool, and after hundreds of kilometers of cutting length, this wear becomes sub-micron wear. Diamond tools also produce thermochemical wear due to oxidation, graphitization, diffusion, and carbonization. The chipping occurs when the stress on the cutting edge of the tool exceeds the local bearing capacity of the diamond tool. It is the most difficult to predict and control damage, and the effect on the quality of the machined surface is greater than the influence of the front and back face wear. Lowering the cutting temperature reduces tool wear. In addition, cutting in a saturated carbon gas can also suppress the carbonization of the diamond tool.
Previous page next page
Gas Spring For Boat,Stainless Steel Gas Spring,Marine Gas Spring,Stainless Steel Gas Lift
Changzhou Juteng Gas Spring Co., Ltd. , http://www.gassprings-china.com